施耐德PLC编程软件全面升级助力智能制造高效革新
19429202025-03-22平板游戏9 浏览
传统工业软件如何突破智能制造的“信息孤岛”?
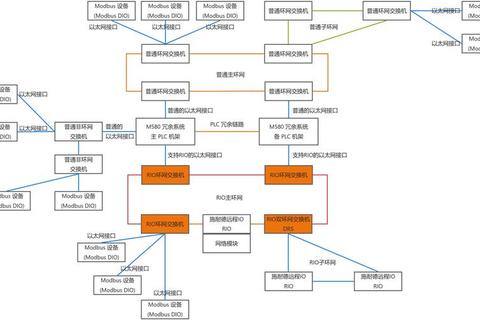
在工业4.0浪潮下,全球超过60%的制造企业仍面临设备协议不兼容、数据流通受阻的困境。当一家汽车零部件厂商试图将1970年代的机床接入数字化系统时,工程师发现这些“沉默的设备”如同被封印的数据宝库——这正是传统工业软件在智能制造时代遭遇的典型困局。施耐德PLC编程软件全面升级助力智能制造高效革新,正在用技术创新打破这堵无形的墙。
1. 开放性能否终结“协议丛林”?
在江苏某新能源电池工厂,施耐德EcoStruxure开放自动化平台成功整合了来自7个国家的23种工业设备。通过支持IEC 61499国际标准和MQTT、OPC UA等12种通信协议,该平台实现了对西门子S7-1200、三菱FX5U等异构设备的无缝对接。这背后正是施耐德PLC编程软件V24.1版本带来的革新——其新增的Modbus TCP/IP转换引擎,使得传统Modbus设备的数据采集效率提升40%。
典型案例显示,某食品机械制造商采用升级后的Control Expert软件,仅用3周就完成了原本需要半年的产线数字化改造。软件内置的协议转换矩阵功能,让1980年代的包装机与2024年的AGV运输车实现了实时数据交互,使整厂设备利用率从68%跃升至89%。
2. 智能化能否重构“人机协作”?
施耐德北京亦庄工厂的实践验证了软件升级的颠覆性价值。通过集成AI模型的M241系列PLC,该厂质检工序实现了从“人眼识别”到“机器视觉”的跨越。软件新增的AI Workbench模块,允许工程师用自然语言描述检测需求,系统自动生成对应的图像识别算法。这使得液晶面板缺陷检测准确率从92%提升至99.7%,误检率降低85%。
更值得关注的是多用户协作编程功能。在山东某智能仓储项目中,来自机械、电气、IT三个领域的工程师通过云端协同平台,实时调试堆垛机的运动控制算法。软件提供的数字孪生环境,让调试周期从传统模式的45天压缩至9天,碰撞测试成本降低72%。
3. 生态化能否重塑行业标准?
施耐德与红帽、英特尔的战略合作,开创了工业软件新范式。三方联合开发的Edge Control解决方案,将PLC编程软件与Kubernetes容器技术深度融合。在广东某PCB制造企业,这种架构使得设备控制程序可以像手机APP般“热插拔”更新,产线切换不同产品型号的时间从8小时缩短至18分钟。
生态力量在四川某智慧水务项目中得到充分展现。通过施耐德PLC软件商店下载的PID优化插件,工程师仅调整3个参数就解决了水泵能耗异常问题。该插件基于200个水务项目的大数据训练,能自动匹配最佳控制策略,使系统综合能效提升15%。
施耐德PLC编程软件全面升级助力智能制造高效革新,正在书写工业自动化的新篇章。对于寻求转型的企业,建议采取“三步走”策略:首先建立设备通信协议档案,其次选择支持多协议转换的中枢平台,最后分阶段实施智能化改造。正如施耐德中国区技术总监所言:“真正的智能制造,不是推倒重建,而是让每台设备都能讲述自己的数据故事。”